10. Land Partition: Step 4
- Jon Pope
- Jul 20, 2023
- 4 min read
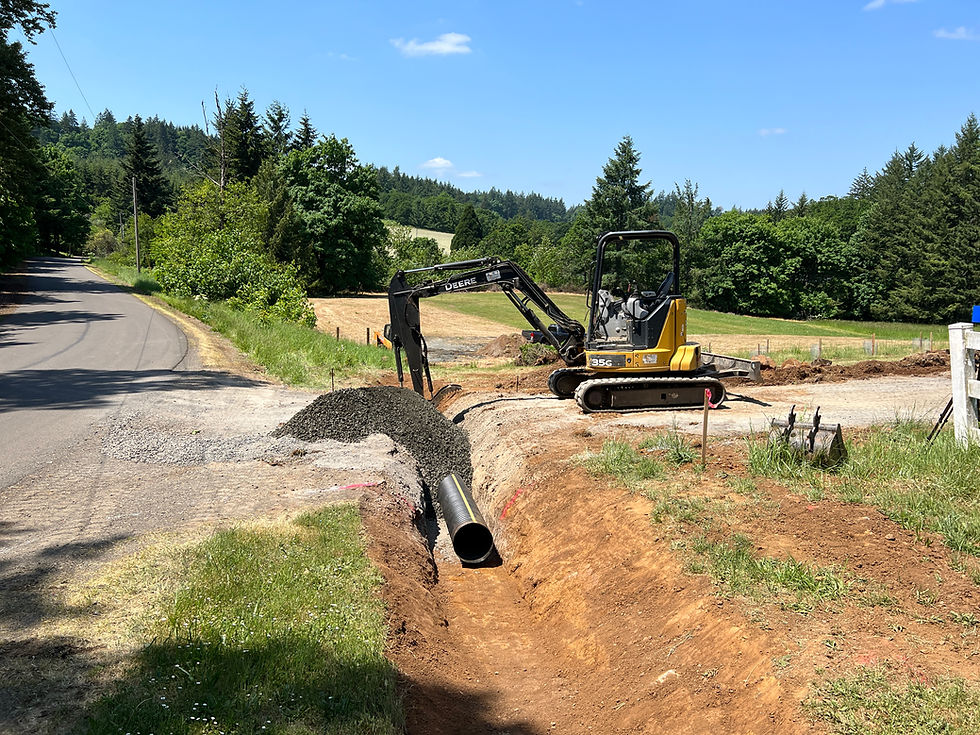
Conditions of Approval
According to the partition approval letter from our county, there are several conditions that must be met before the partition can be completed. Most of the conditions are items which will be completed by our surveyor, but one requirement was within my capabilities to accomplish: The county’s Land Development Engineering and Permit (LDEP) department requires the entrance to our driveway to be 20 feet wide as measured at the right-of-way/property line. I think the requirement comes from engineering standards developed for roads serving more than 1 property. I also learned that there are specific requirements for emergency vehicles which likely has some impact on this condition.
Driveway Widening
Prior to modification, the entrance measured approximately 15 feet at the right-of-way and tapered down to 12 feet wide for the length of the driveway. Even though the county only requires the entrance to be widened, I had already desired to increase the driveway width to around 15 feet which will serve these two properties well. A 12-foot-wide driveway may have been satisfactory for previous owners but is slightly narrow for large trucks & trailers. A narrow road also gives no room for two cars to pass each other when coming and going.
The first step in this mini project was to submit an application for an Access Permit. I printed the application from the county website and filled out the applicable information. I also had to submit a site plan showing the proposed modifications. Since this was such a simple job, minimal details were included.
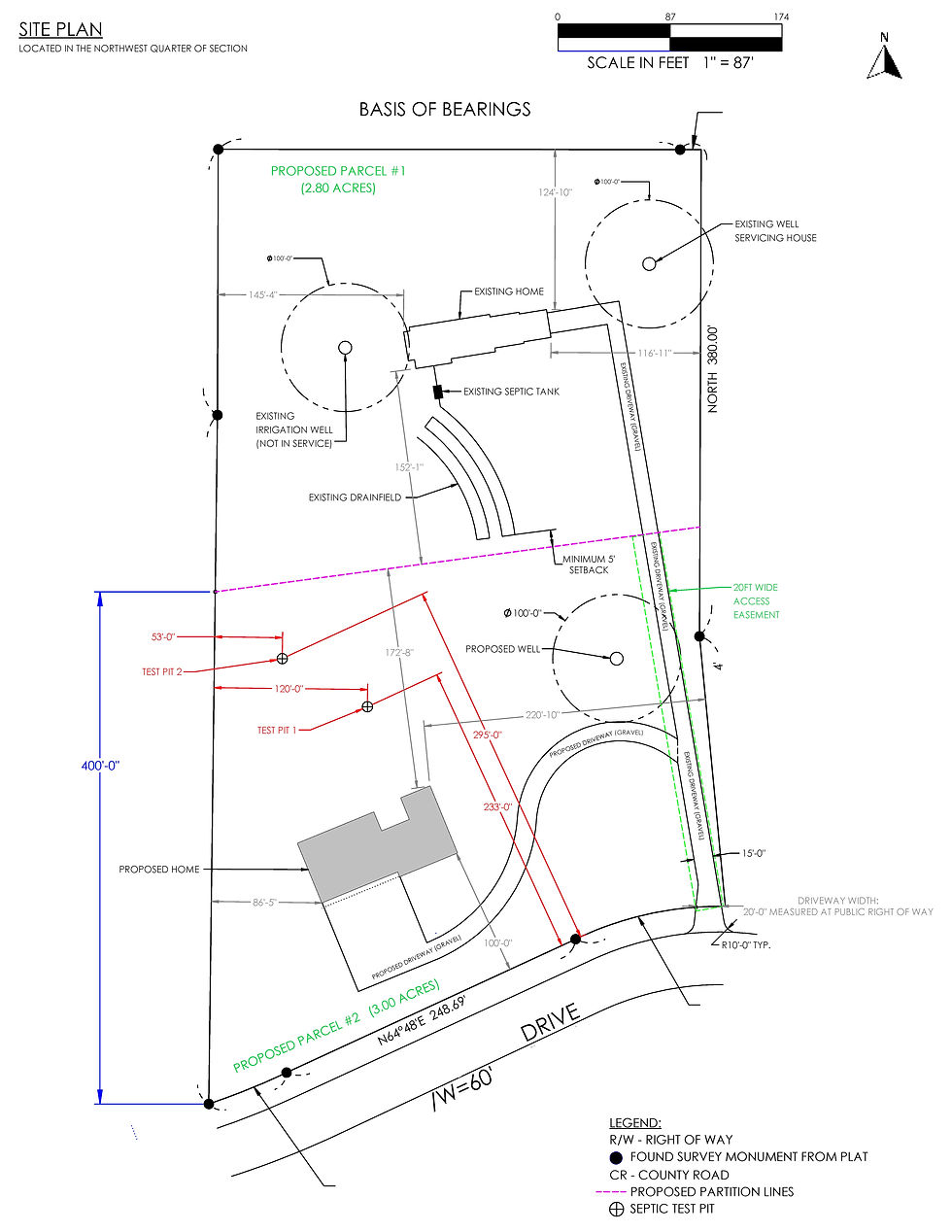
After submitting the application at the public works building and paying the $50 permit fee, I waited 5 days to receive the approved permit in the mail. The permit came with a little blue placard which got posted at the road for project identification by the inspector.
The permit indicated that a new culvert was required and needed to be 12-inch diameter at a minimum. Approved materials would be concrete, HDPE, or ductile iron. I was hoping to simply add an additional length of concrete culvert to the existing, but after calling several material suppliers in my area, it was clear that concrete culverts are either obsolete, or very tough to get your hands on. The new standard for culverts is double wall HDPE plastic pipe and comes in 20-foot lengths. This product was readily available from multiple supply houses and at a reasonable price.
Upon review of the county’s “Driveway Construction Standards” document, I discovered that HDPE culvert requires at least 12 inches of backfill on top of the pipe. The concrete pipe in the existing driveway had maybe 3 to 4 inches of gravel cover. I had two options: use ductile iron pipe which there is no minimum cover depth, or bed the plastic corrugated pipe much deeper than the existing culvert. Since iron pipe would be much more expensive, if available at all, I chose the 2nd route.
I had the permit in hand and a plan to execute. With a week of P.T.O. from my day job, I picked up the rented excavator and started ripping out the old culvert. My hope was to have the digging completed on a Monday night, call for the initial inspection on Tuesday and have the driveway covered by Tuesday night. This would leave our driveway out of commission for only 1 day which I thought was reasonable. Unfortunately the digging took a little longer than expected which extended the driveway down-time to 2 days, but we made it work.
Once the trench was completed and ditches re-shaped on each side, I placed the pipe and scheduled the pre-cover inspection. After passing the inspection, I grabbed a couple loads of ¾ minus gravel in my dump trailer just to get the trench covered so that we could use our driveway again.
The urgent action to cover the driveway was complete so I switched gears and excavated the rest of the driveway. I removed 6-8 inches of soil from the side of the driveway to a width of about 15 feet and placed geotextile fabric down on the exposed dirt. I know it is a highly debated topic whether the fabric is needed or not, but its cheap insurance against settling in the future.
One thing I overlooked was availability of gravel suppliers. I was thinking a couple days notice was enough time to get a truckload of gravel delivered, but after making some calls, it wasn’t looking good. I finally found one company that was able to deliver two 16 yards loads on a Saturday. Fortunately, this was just enough to get a rough grade on all excavated areas. Once the gravel was down, I used the skid steer to level the new road as best as possible. I made a few passes on the new rock with a reversible compactor and called for the final inspection.
Access permit application fee: $50
Excavator rental (3.5 days plus fuel): $495
Compactor rental (2 days): $299
2x 20’ sections of culvert pipe: $482
75’ x 15’ geotextile fabric: $50
40 yards of ¾” minus quarry rock: $1,610
Partition costs to this point: $12,946
Comments